Worldwide Support
Over 25 distributors and support centres worldwide
Flexible maintenance contracts
Tailor made plant specific contracts with 24Hr Support
30 years experience
Developing, manufacturing and installing
Are You Using Bag Filters to Control Dust Emissions?
Power plants, cement plants, steel plants, smelters, asphalt plants, incinerators, food manufacturers, chemical producers, pharmaceutical producers, and other industrial companies are widely using bag filters to control dust emission. Moreover, in some applications, bag filters are also employed to capture other products coming out of mills, such as cement, coal, and other raw materials.
Fabric filters are, without doubt, an extremely efficient pollution control device with the ability to capture over 99% of dust collected from process gas. However, they have one drawback: they are prone to leaks.
To maintain ongoing performance, periodic filter bag replacement, as well as filter inspection and monitoring, is crucial. The optimum timing for a filter bag replacement should maximize the bag’s lifespan while taking place before a significant leak event occurs. Such a leak could result in exceeding emission limits and cause the process to stop.
An accurate prediction for bag replacement can be achieved with the aid of a continuous leak detection system. The advantage of this system is that the replacement or maintenance of a bag filter can be routinely planned, rather than having to stop a process due to the immediate necessity to replace a filter bag. This can result in significant cost savings, particularly when capturing products.
CODEL’s ET301 Triboelectric Sensor has been successfully applied to numerous bag filter leak detection applications. For instance, six ET301 sensors were installed on six modules of semi-dry NID™ FGD. Each module consists of an FGD reactor and a fabric filter, which serve as the final pollution control device. Outlet ducts from the six FGD modules merge into one duct before entering the stack.
CODEL ET301 sensors are fitted on the outlet from each module, allowing independent monitoring of the bag filters. Consequently, this enables operators to schedule maintenance more effectively and isolate leaking bags without stopping the plant.
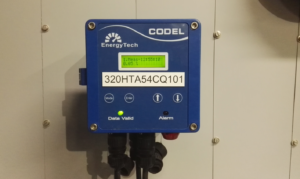
What are the main features of the ET 301 leak detection sensor?
- Capable of detecting the smallest levels of dust, below 0.1mg/m3
- Capable of detecting particulates in a size range of 0.1 to 100µm
- Fast response time
- Easy networking for multi compartments and modular arrangements. RS 485 MODBUS and 4-20A output.
- Minimum maintenance requirement
- Simple installation, no alignment required
- No optical surfaces, purge air not required
- No interference with other measurements
What are the customer benefits?
- Prevents loss of product on some applications. Post mill location, the bag filter is used to capture product.
- On multi-compartment bag filters our modular arrangement allows for the leaking part of the bag house, or leaking module to be identified.
- When the ET301 output data is correlated with the fabric filter cleaning routine data it can be used to identify a leaking row in the bag house.
- Helps to extend operation lifetime of bag filters safely. Manufacturers of bag filters recommend a bag replacement approximately every 1.5 years. However, close monitoring of the bag filter can extend this lifespan safely which results in reduced maintenance.
- Allows for a reduction in visual inspection of the filter frequency.
Click here if you would like more information on CODEL’s ET301
Ask a question
For further information on any of our products, please complete our enquiry form and a member of staff will respond as soon as possible.
You can also call: +44(0)1629 814351